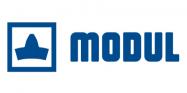
Gear Hobbing
H400
Max. workpiece diameter | mm | 400 |
Max. module | mm | 8 |
Radial movement (Х) | mm | 60-285 |
Max. radial feed speed | mm/min | 10000 |
Tangential movement (Y) | mm | 240 |
Max. tangential feed speed | mm/min | 7000 |
Axial movement (Z) | mm | 200-600(200-800) |
Max. axial feed speed | mm/min | 7000 |
Milling spindle rotary speed | rpm | 225-1800(300-3000) |
Milling spindle drive power | kW | 14(31) |
Milling spindle nominal torque | Nm | 550(190) |
Milling head swivel angle | grad | ±45 |
Tool clamping arbour fixture taper | ? 32/SK25 | |
Max. mill diameter | mm | 175(130) |
Max. mill length | mm | |
Max. table rotary speed | rpm | 1-400 |
Table diameter | mm | 330 |
Table hole diameter | mm | 100 H7 |
Total connected load | kW | 40 |
CNC system | Siemens 840 D Solutionline | |
Quantity of controlled CNC axes | 6 | |
Weight | Kg | 9500-11000 |
Overall dimensions (L х W х H) | mm | 4000x2420x2750(3050) |