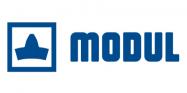
H200
Max. workpiece diameter | mm | 200 |
Max. module | mm | 4 |
Radial movement (Х) | mm | 60-150 |
Max. radial feed speed | mm/min | 10000 |
Tangential movement (Y) | mm | 200 |
Max. tangential feed speed | mm/min | 7500 |
Axial movement (Z) | mm | 100-450 |
Max. axial feed speed | mm/min | 10000 |
Milling spindle rotary speed | rpm | 250-3500 |
Milling spindle drive power | kW | 15 |
Milling spindle nominal torque | Nm | 190 |
Milling head swivel angle | grad | ±45 |
Tool clamping arbour fixture taper | ?22, 27, 32 / SK25 | |
Max. mill diameter | mm | 90 |
Max. mill length | mm | 285 |
Max. table rotary speed | rpm | 10-1000 |
Table diameter | mm | 132 |
Table hole diameter | mm | 80 Н7 |
Total connected load | kW | 35 |
CNC system | Siemens 840 D Solutionline | |
Quantity of controlled CNC axes | 6 | |
Weight | Kg | 6500-8000 |
Overall dimensions (L х W х H) | mm | 2300x2600x2850 |
The H 80/160/200 series is the second platform of our smallest hobbing machine line for automotive applications. These machines have been designed for dry cutting applications in particular, though using oil or emulsion is no problem. Chips are conveyed cleanly from the work area by means of a chute, which is steep and smooth in design to prevent any build up. The hob head is housed within the tool column, which is tightly fastened to the sturdy machine bed. The tailstock is located on the tool column above the hob head, leaving the work area remarkably free for workpiece loading and unloading operations. To cater for your line automation needs, the machine is available with a standard, direct-driven double gripper loader. Placing a machine in close proximity to your workpiece conveyor belt, in fact, requires no further automation other than that provided by the completely integrated solution. All peripheral units are easily accessible and maintenance-friendly (including pneumatics, hydraulics, electrics and chip disposal).
Moreover, the direct drive technology incorporated in this series makes your machine a safe investment over time, since any future tool developments can be fully exploited.
Fast and easy operator guidance throughout the whole process is guaranteed by our latest dialogue software on the Siemens Sinumerik 840 D control with the possibility to make flexible tooth flank.