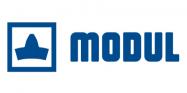
Gear Hobbing
H160
Max. workpiece diameter | mm | 160 |
Max. module | mm | 4 |
Radial movement (Х) | mm | 45-135 |
Max. radial feed speed | mm/min | 10000 |
Tangential movement (Y) | mm | 200 |
Max. tangential feed speed | mm/min | 7500 |
Axial movement (Z) | mm | 100-450 |
Max. axial feed speed | mm/min | 10000 |
Milling spindle rotary speed | rpm | 250-3500 |
Milling spindle drive power | kW | 15 |
Milling spindle nominal torque | Nm | 190 |
Milling head swivel angle | grad | ±45 |
Tool clamping arbour fixture taper | ?22, 27, 32 / SK25 | |
Max. mill diameter | mm | 90 |
Max. mill length | mm | 285 |
Max. table rotary speed | rpm | 10-1000 |
Table diameter | mm | 132 |
Table hole diameter | mm | 80 Н7 |
Total connected load | kW | 35 |
CNC system | Siemens 840 D Solutionline | |
Quantity of controlled CNC axes | 6 | |
Weight | Kg | 6500-8000 |
Overall dimensions (L х W х H) | mm | 2300x2600x2850 |
The H100 is used in small and large batch production in automotive and general engineering industries. Rigid and thermally stable bed provides damping of vibrations during processing. Range of operations can be widened due to integration of technologies into the machine.
Features